Garrard 301 Restoration
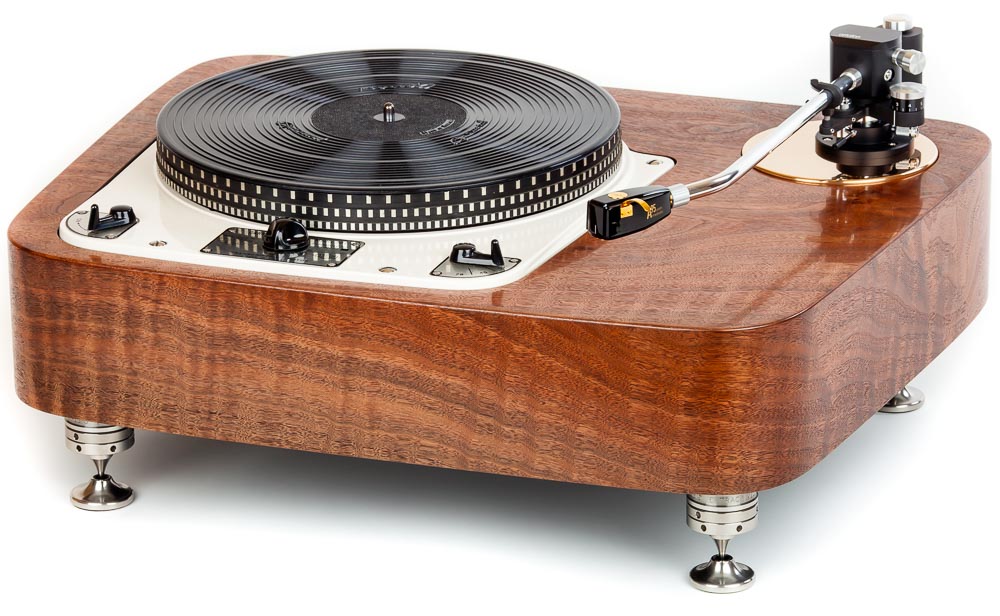
Whether you are just beginning a Garrard 301 based deck, if this is your third, or hundredth, or if you have owned your 301 for many years, and are now ready to bring it to it’s full potential, we can help. We are here to help you see your Garrard and Thorens based projects become reality, and with as much ease as possible. We can turn your Garrard 301 into a ‘giant killer’ which will hold it’s own, and excel along side the best of the best in turntables.
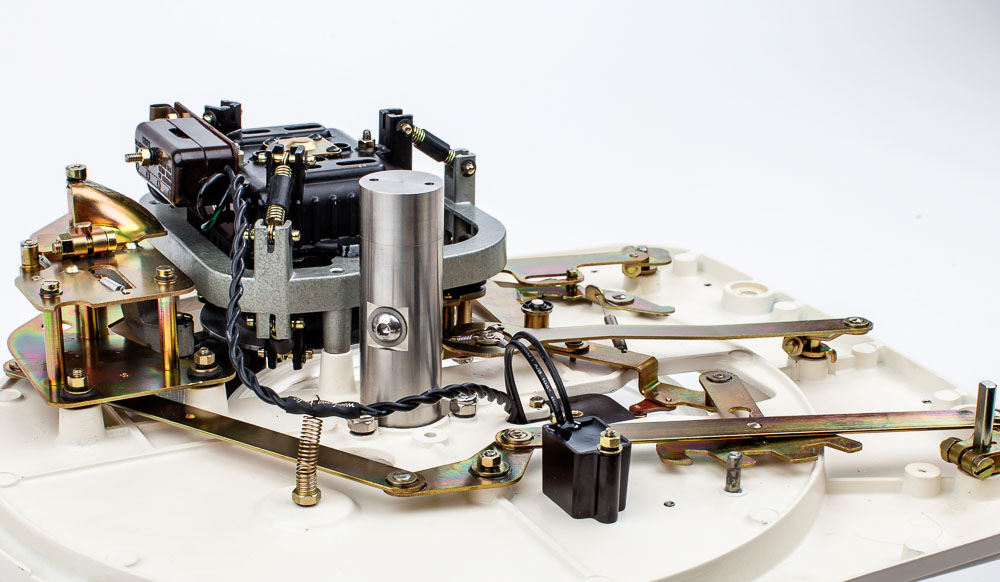
All work that we do is backed by a limited 2 year warranty on labor and installed parts. After we service your deck, you can expect many years of trouble-free operation.
- On arrival at our facility, your 301 is inspected to confirm that it travelled safely, and to assess it’s current condition. We generally contact you immediately after unpacking and inspection.
- The unit is fully disassembled down to the bare chassis, the motor, main bearing, all assemblies, linkages and knobs are disassembled.
- The chassis is thoroughly cleaned and polished, Cream enamel chassis’ and Hammertone chassis’ are treated differently to preserve the original sheen and quality of each finish. This level of cleaning of the chassis yields results that amaze us in most every single case.
- Linkages, hardware, and other parts are deep cleaned in our powerful ultrasonic tank.
- The motor is completely disassembled. All parts are carefully inspected. The motor bushings and rotor axle journals are measured with highly precise measuring equipment. The tempo linkage pivot is checked to be sure that it is parallel with the motor spindle, as these are sometimes bent from poor handling. It is replaced if necessary. We stock new pressed sintered bronze bushings and will advise you if they need to be replaced. We use a multi-step process to fully clean the old oil and residue from the old sintered bronze bushings, and recharge them with the correct lubricant in a vacuum chamber. A new motor thrust ball bearing is installed. New lubricating felts are installed. The thrust end of the motor shaft is inspected, and resurfaced if necessary. The wiring harness and wiring block terminals, solder joints are inspected. The motor shaft is carefully micro polished by hand. Your motor is reassembled, and checked for correct operating speed, and adjusted as necessary for ideal long term, quiet running performance.
- Electrical switch contacts are inspected and cleaned, and replaced when necessary.
- New springs are installed throughout.
- New motor suspension spring dampers are installed. This is an important step that some other builders overlook.
- New up-rated spark suppressor is installed.
- Eddy brake disc is checked for flatness, replaced if necessary, and carefully set at the correct height.
- A new precision CNC machined drive pulley is installed
- Idler wheel axles are micro polished, new idler wheel bushings are installed and aligned correctly, and the idler wheel edge is cleaned and dressed. The idler wheel thrust plate is reversed, giving a new bearing surface, and re-installed using rivets.
- New Idler Tower isolating grommets are installed.
- Main Spindle Bearing is micro-polished, the housing cleaned, sintered bushings are recharged with lubricant.
- Main bearing oil gallery plugs are sealed with epoxy to prevent oil leaks (this is important as we have seen some that leak.
- Main bearing is lubricated with the correct lubricant, and sealed against leakage. We can make your bearing so it does not leak.
- Plated metal linkages and hardware are treated with a protectant to help prevent corrosion and rust.
- During installation, all sliding or rotating surfaces are lubricated with top quality, application and viscosity specific lubricants.
- The platter internal drive rim is cleaned and checked for anything which could cause mechanical noise.
- After your deck is re-assembled, it is ‘run in’ over the course of several days, during which it is closely observed for quiet, correct, and speed accurate operation. Adjustments are made as necessary to bring your deck back to it’s full potential.
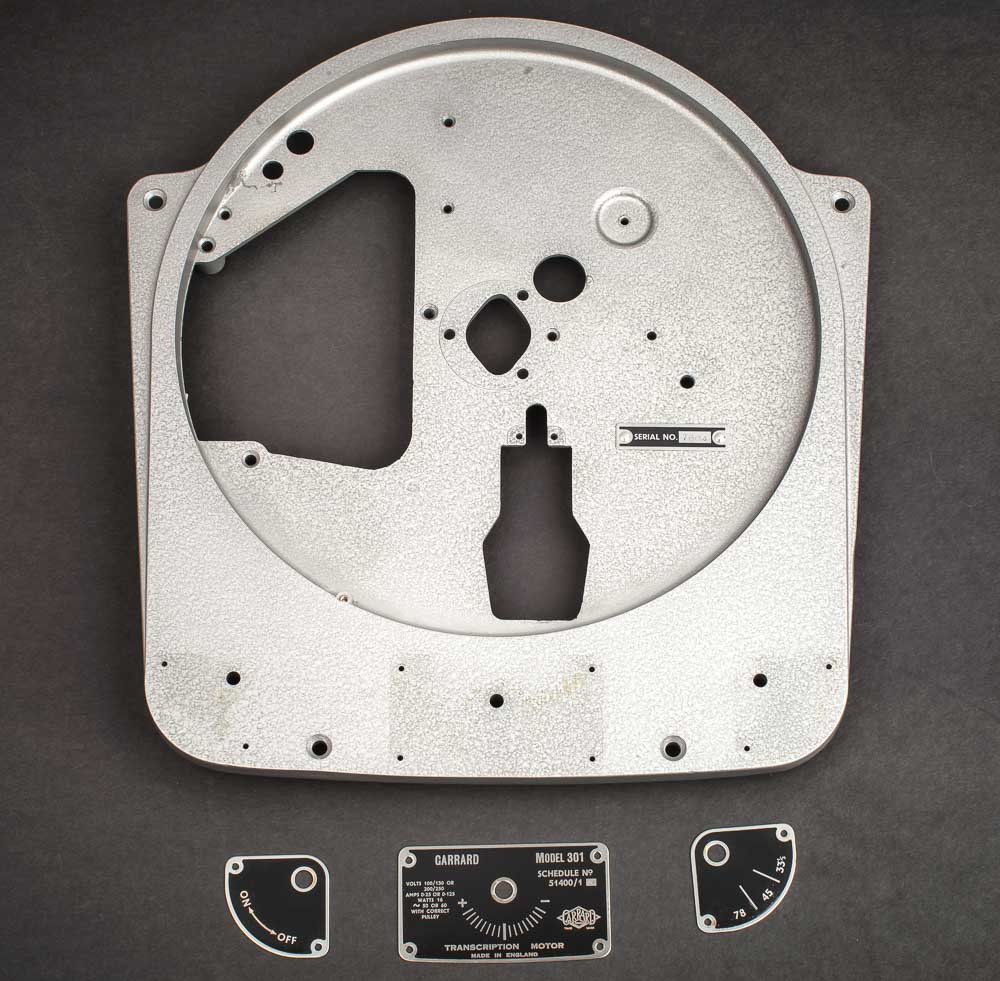
We start by completely disassembling the deck all the way to the bare chassis. This enables complete access for cleaning the enameled finish. On most rebuilds we remove the name plates, as over the years, most decks have built up residue right at and just under the name plates, and some have even developed light scratches which we can polish out by removing the name plates. To replace, we use rivets which match the original rivets.
We have a unique approach to chassis cleaning and polishing for each the original Hammertone finish, and the original cream enamel finish. In all cases, we see massive improvements. We have a ‘leave no trace’ approach to chassis cleaning and polishing, maintaining and preserving the essential qualities of the original finish.
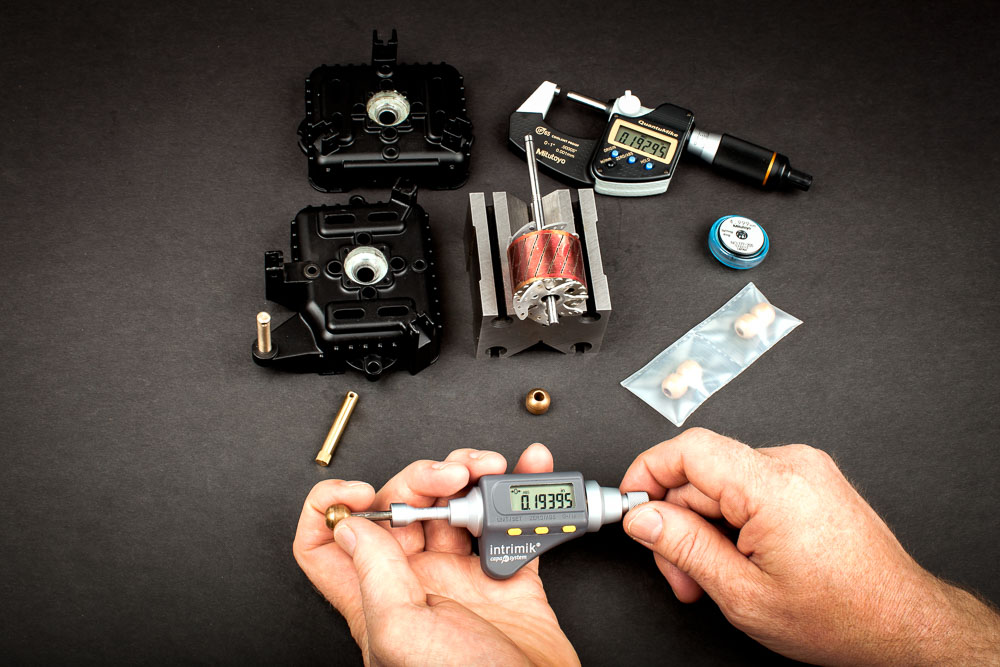
Measuring Motor bushings and motor spindle diameter to ensure the correct running tolerance for the motor shaft. New pressed sintered bronze bushings are installed when necessary. Bushings are flushed and impregnated with new lubricant in a vacuum chamber.
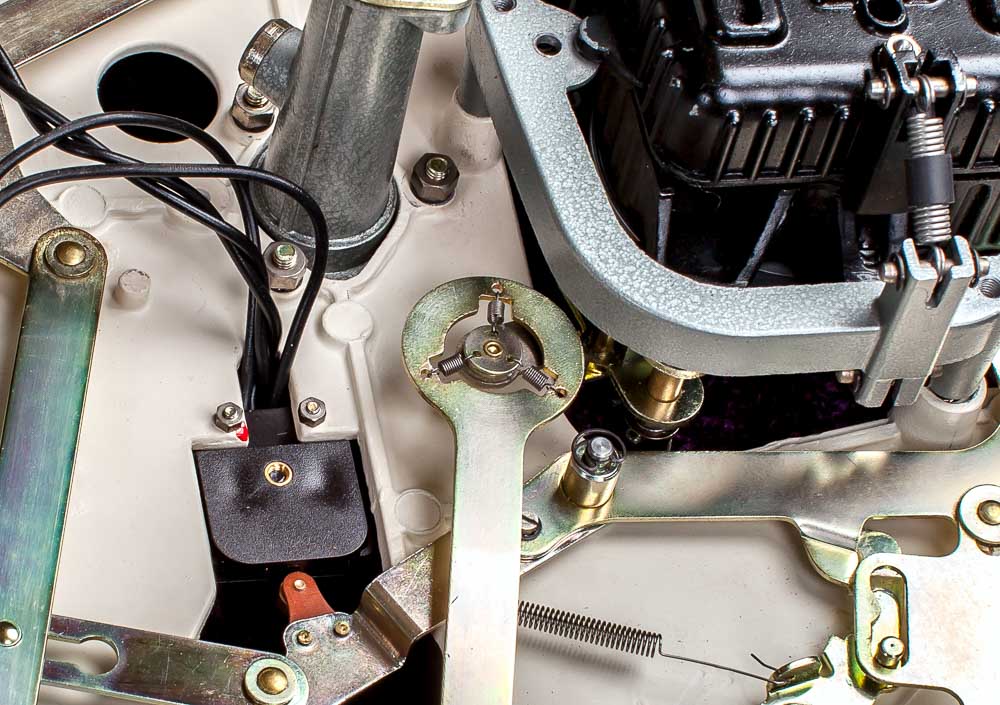
The 3 tempo linkage springs are commonly stretched or damaged, as are the motor carriage suspension springs. We replace all springs, and also the motor suspension spring rubber dampers. These dampers are commonly overlooked, but very important.
Occasionally, the rivet which acts as the pivot for the tempo linkage is too tight, causing poor quality of operation. We always check this and adjust when necessary.

For the Hammertone Garrard 301, we remove the contents of the original ‘can style’ spark suppressor, and ‘re-pot’ up-rated modern components into the original ‘can’. We always replace the spark suppressor during a Garrard 301 restoration.
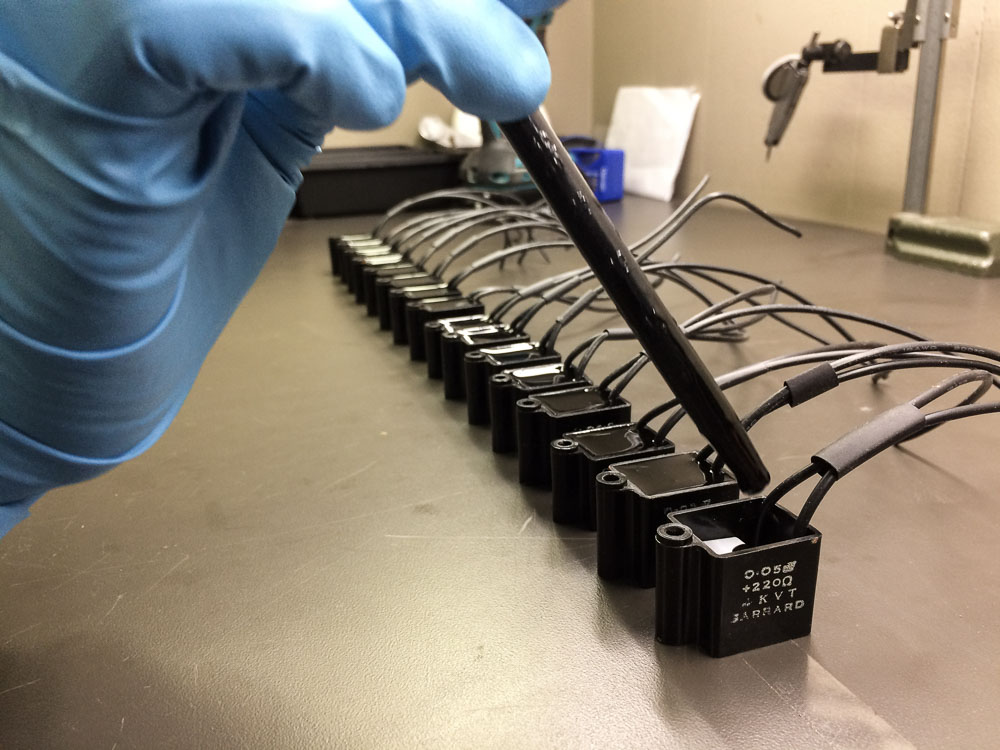
We save old spark suppressors, and when possible, we remove the old components and re-pot them with up-rated components. This helps to maintain the vintage element to the deck, while bringing this important component back to full functionality, and better than original. After 50 years, capacitors need to be replaced. An old spark suppressor can go bad at any time, and when it does, your turntable will stop working correctly. For this reason, we always replace the spark suppressor by un-soldering the leads from the contacts, and solder a new one in. If the original contacts are worn, or are bent, we replace them.
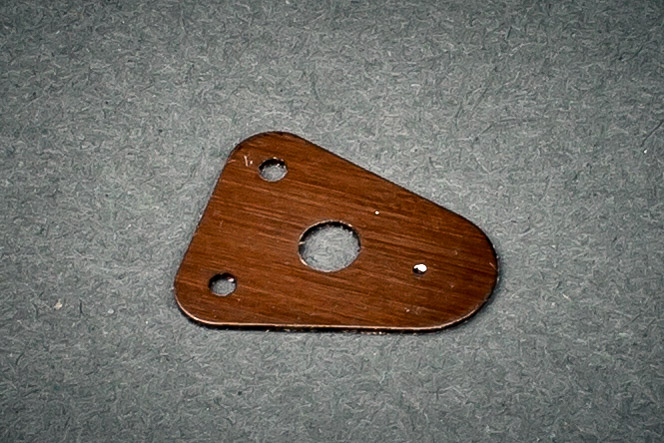
This is the ‘thrust plate’ surface which acts as a thrust bearing for the Garrard 301 idler wheel. During our restoration, while removing and replacing the old idler wheel bushings, we remove this plate and reverse it, revealing a fresh bearing surface. The dimpled worn spot in the end of the thrust plate is a wear mark from the thrust end of the idler wheel axle. A fresh bearing surface here makes an important improvement in idler wheel performance and overall speed stability.
We offer a new CNC machined eddy brake disc, machined from stress relieved 6061-T651 aircraft aluminum that is much more precise than the original.
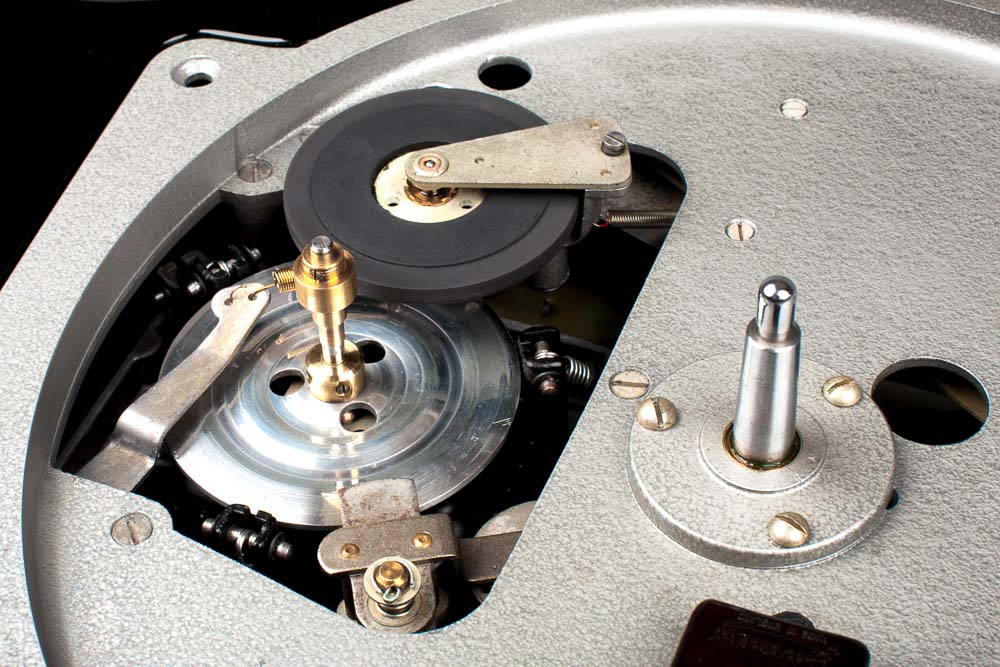
Idler wheel is checked, new idler wheel bushings, etc.
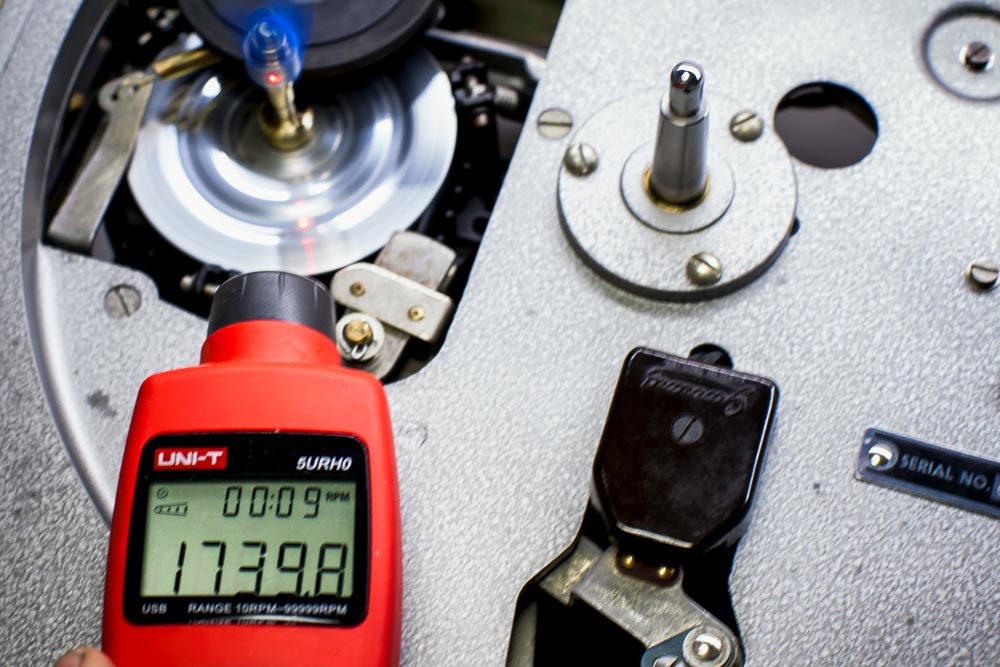
Motor speed is confirmed and set to 1740rpm at operating temperature
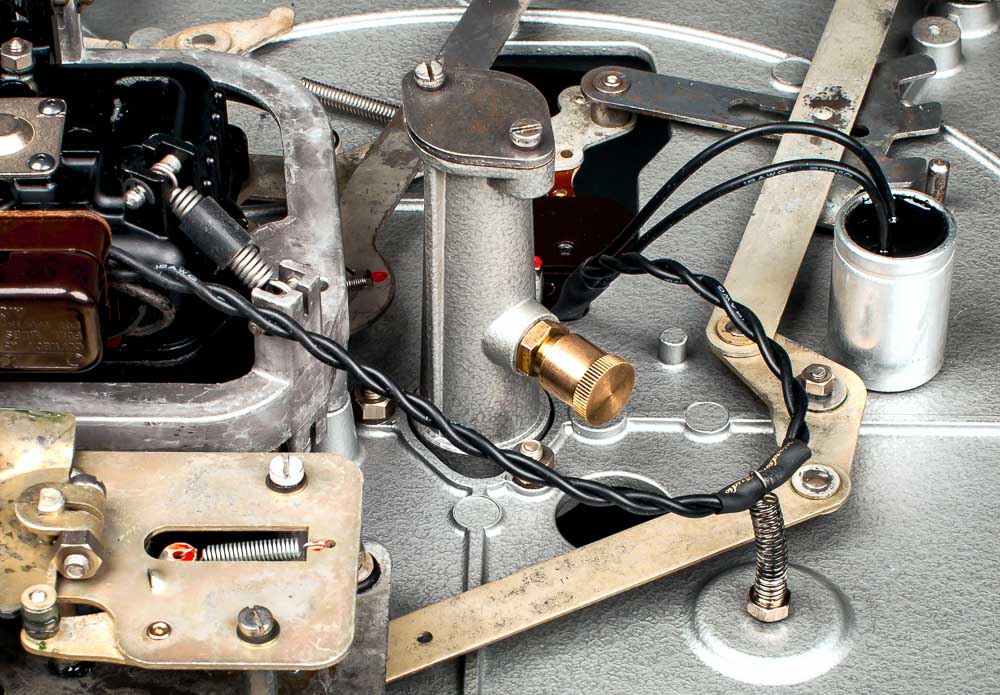
When necessary, or when requested, we install a new wiring harness made from highly flexible high temperature silicone wire
We have good stock of original hardware including nuts, screws, and washers, knobs and face plates to replace missing or damaged pieces on your deck. Over the years, most of these decks have been worked on by folks who inadvertently missed a few washers here or there. Your deck will be returned to you complete and correct, as it should be.
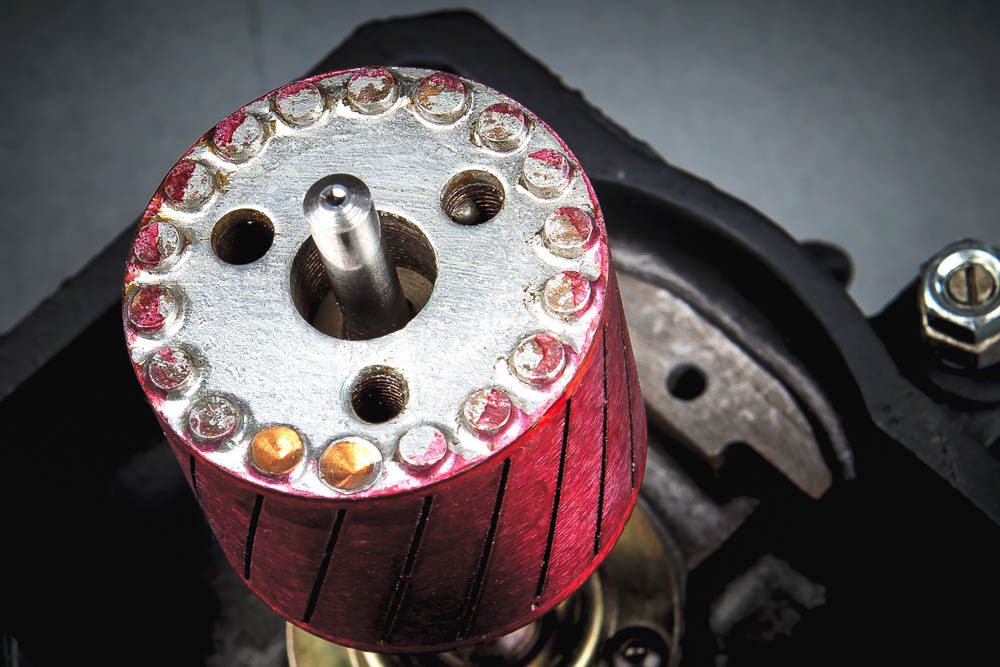
Here, the thrust end of the motor spindle is worn. We resurface this when necessary.
During the final tuning, the speed is set so that the tempo knob is very close to dead center on the scale at 33, 45, and 78rpm, and the motor spinning at 1740 rpm. (60hz)
We can install a new power cord on request , but we do not use, nor recommend a standard power cord for the Garrard 301. A typical power cord attached directly to the motor is a path for mechanical noise into the plinth, it can disrupt the correct operation of the suspension, and also is a liability in that, if accidentally yanked, it can damage the wiring block mounting plate and require costly repairs. Instead, we make a highly flexible wiring harness that terminates at an IEC AC inlet mounted on your plinth. We can provide this setup for you at additional cost after you provide us with the necessary details of your particular setup. This is the ideal method for powering a Garrard 301 or 401 idler drive turntable.We offer unsurpassed quality in custom automotive finishes for your chassis and platter, professional ‘color sanding’ finish polishing, as well as yellow zinc plating for linkages in an AC7004 certified precious metals lab on special request. Please contact us for details.We offer unsurpassed quality in custom automotive finishes for your chassis and platter, professional ‘color sanding’ finish polishing, as well as yellow zinc plating for linkages in an AC7004 certified precious metals lab on special request. Please contact us for details.
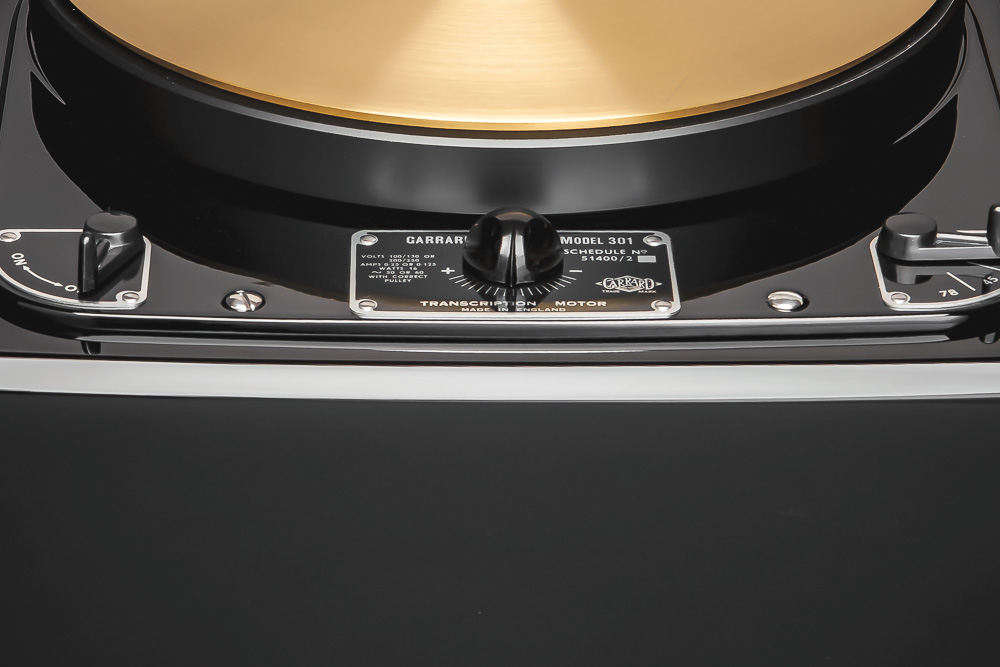
We offer unsurpassed quality in custom automotive finishes for your chassis and platter, professional ‘color sanding’ finish polishing, as well as yellow zinc plating for linkages in an AC7004 certified precious metals lab on special request. Please contact us for details.